Fábricas de coraje frente a la crisis sanitaria
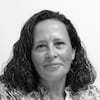
La industria española se ha contagiado de una cadena de solidaridad. Factorías aeronáuticas, automovilísticas, cosméticas, textiles o cerveceras se reconvierten a toda velocidad para contrarrestar el desabastecimiento de material sanitario. Entramos en sus renovadas plantas de producción
Cómo vamos acoser con guantes y mascarilla? ¡Eso es imposible!”. Una semana después de decretarse el estado de alarma y ante la acuciante carencia de material sanitario de protección, esa pregunta corría por las instalaciones de la Sociedad Textil Lonia, fabricante de las marcas Purificación García y Carolina Herrera, en Pereiro de Aguiar (Ourense). Sus costureras, bregadas en el trabajo artesanal, se sentían incapaces de enfundarse las manos y seguir siendo tan diestras como siempre. Pero no había más remedio. La urgencia no perdonaba. Tampoco las ganas de ayudar. La pandemia se extendía sin dar tregua, los hospitales se habían saturado y su personal estaba a merced de la covid-19 por falta de equipos de protección individual, esos EPI que se han hecho desgraciadamente tan familiares entre los españoles.
FOTOGALERÍA: Contagio de solidaridad en la industria española
En Pereiro de Aguiar se pusieron a la faena, contactaron con las autoridades para recabar información sobre las necesidades más urgentes. Para responder a ellas lo antes posible, mantuvieron reuniones con los hospitales cercanos, se enteraron de los materiales que tenían disponibles estos centros para poder fabricar los productos a toda prisa, hicieron prototipos, una prueba piloto y comenzaron a cortar tejido, confeccionar patrones y a producir mascarillas y batas de protección para los trabajadores de las unidades de cuidados intensivos (UCI) sin tener la planta adaptada. La velocidad era crucial.
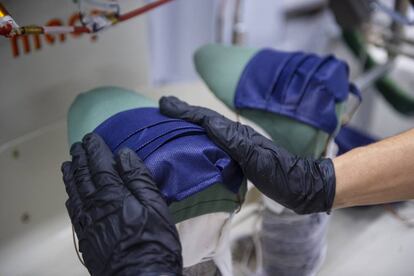
“Empezamos con una fabricación lenta porque teníamos que ajustar las líneas de producción, formar a la gente y localizar el aprovisionamiento, que fue lo más difícil de todo”, recuerda uno de los responsables de producción de la compañía. Después la maquinaria adquirió un ritmo vertiginoso. “Arrancamos con 2 batas, al día siguiente hicimos 30, al otro 60 y luego fuimos doblando a un solo turno y con personal voluntario hasta alcanzar unas 600 batas diarias y unas 3.000 mascarillas. Lo que conseguimos en solo una semana fue increíble”.
Sociedad Textil Lonia representa uno de los crecientes ejemplos de compañías industriales que han reconvertido su actividad y han puesto su capacidad de fabricación al servicio de la contención del coronavirus, cuyo punto más débil ha sido la carencia de equipos de protección individual y la falta de respiradores para atender a los pacientes, que conforme se agigantaban las cifras de contagios resultaba más acuciante.
Con las UCI de los hospitales de Madrid y Barcelona desbordadas e incapaces de procurar respiradores a todos los pacientes que los necesitaban, Seat decidió coger el testigo y contactó con los hospitales Germans Trias y Clínic de Barcelona para industrializar los ventiladores OxyGEN de la empresa Protofy.xyz, que había desarrollado el prototipo y buscaba industrias para fabricarlo. La firma automovilística asumió el reto utilizando piezas de sus coches para que el proceso fuera más rápido.
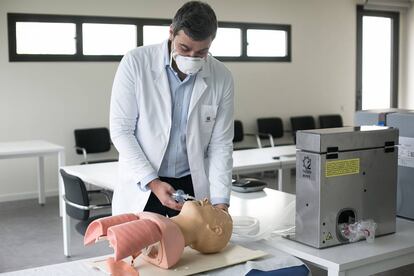
Las cajas de los respiradores llegaron de Seat Barcelona, donde las cortadoras láser ajustaban la chapa para luego montarla en la factoría de Martorell. “Modificamos el chasis del Seat León para hacer el ventilador automático y cogimos el motor del limpiaparabrisas para que impulsara la caja de ventilación”, cuenta Alicia Molina, responsable de ingeniería de procesos de presas y chapistería de la marca, que resalta que en solo dos semanas y media consiguieron homologar el respirador de emergencia. “Un tiempo récord”, subraya.
La noche del sábado 4 de abril, después de adaptar la fábrica a su nueva actividad y preparar a 30 personas para abordarla en un turno de producción, salieron las primeras dos furgonetas con los ventiladores de emergencia hacia hospitales de Madrid y Barcelona. Entonces la planta de Martorell estaba parada, con 10.500 de los 14.800 trabajadores de Seat integrados en un expediente de regulación temporal de empleo (ERTE). Aunque más de 150 personas participaron en el proyecto “día y noche porque estábamos muy entregados”, asegura la ingeniera.
El 10 de abril, la compañía suspendió la producción aduciendo que “la situación en las UCI ha mejorado como consecuencia del descenso en el número de casos positivos de covid-19 y los hospitales no necesitan por ahora más respiradores de emergencia”. Había fabricado 600.
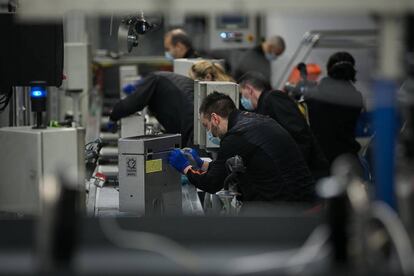
Pero eso todavía no ha sucedido con los equipos de protección individual, que, aunque empiezan a llegar a hospitales, centros sanitarios y residencias de la tercera edad con mayor asiduidad que hace algunas semanas, tienen a muchas empresas embarcadas en su elaboración porque la necesidad continúa. Y además, como explican en Textil Lonia, “cada vez nos llegan más peticiones de hospitales, residencias de la tercera edad e incluso de empresas, que se han enterado de que las estamos realizando, nos las piden y es frustrante no poder dar abasto”.
En la Agencia Española de Medicamentos y Productos Sanitarios (AEMPS) lo saben. “Agradecemos todas las iniciativas de colaboración de empresas no sanitarias que están ayudando a abastecer a la población de los productos necesarios para hacer frente a la covid-19”, señala el organismo dependiente del Ministerio de Sanidad, que añade que las necesidades vienen muy determinadas por la situación en cada momento. Ahora es algo menor la de respiradores; sin embargo, la de mascarillas o geles seguirá siendo vital durante la etapa de desescalada del estado de alarma.
La Agencia explica que ha recibido iniciativas de colaboración de empresas de todos los sectores, unos proyectos que también se desarrollan desde las comunidades autónomas y desde las propias compañías. En las dos últimas semanas, indicaba el pasado 22 de abril, se habían solicitado 53 licencias de fabricación temporal de mascarillas y batas quirúrgicas, de las cuales una docena habían sido autorizadas mediante un procedimiento excepcional arbitrado para agilizar la tramitación ante la emergencia sanitaria, como la producción de respiradores-ventiladores a siete empresas y la de geles y soluciones hidroalcohólicas a nueve.
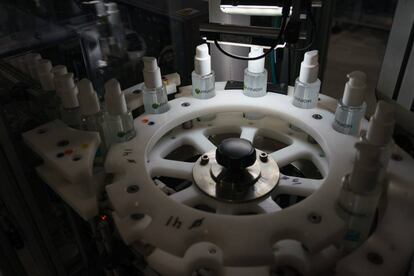
La fábrica de la multinacional L’Oréal en Burgos es una de ellas. A mediados del mes de marzo recibió el permiso e inició la tarea de reconvertir sus fórmulas para elaborar geles hidroalcohólicos y poner en marcha el aprovisionamiento. “Al principio no teníamos frascos para estos geles, con lo que decidimos utilizar los que usábamos para otros productos”, cuenta Benoît Mocquant, director de la planta. Después los compraron y ampliaron los formatos de sus soluciones higiénicas, desde envases individuales hasta botes a granel. “Así podemos responder a todas las necesidades”, destaca. Primero llegaron a los hospitales y residencias de mayores cercanas y posteriormente implementaron una organización más estructurada, con entrega directa e indirecta, también para los cuerpos de Seguridad del Estado.
La fabricación masiva arrancó el 20 de marzo, con 50 personas participando activamente y orgullosas de su nueva función solidaria. Dedicaron 3 líneas de producción que después fueron 7 del total de 44 de la factoría. Desde entonces han elaborado 183.700 litros de geles desinfectantes y envasado 753.000 botes, a razón de 30.000 unidades diarias.
Tras el parón obligatorio de la Semana Santa, la fábrica burgalesa de L’Oréal iniciaba la vuelta a la normalidad, si puede llamarse así a la situación que vive actualmente la industria, con una actividad más que mermada como consecuencia del coronavirus. Allí los geles hidroalcohólicos siguen fabricándose sin descanso, mientras se impulsan las líneas de producción de champús y otros productos de higiene personal.
L’Oréal seguirá elaborando estos líquidos hasta que los fabricantes especializados puedan preparar los suficientes para abastecer al mercado. Mocquant calcula que lo harán al menos hasta el mes de junio.
Fuera de las factorías especializadas, las pantallas de protección facial son probablemente el producto que más se está produciendo a iniciativa de las empresas. Y ello es gracias a la impresión 3D, presente en multitud de compañías tengan la actividad que tengan. Cruzcampo fue una de las primeras en pasar a fabricarlas noche y día durante los siete días de la semana tras decretarse el estado de alarma. Después de comprobar con las autoridades sanitarias que, entre las carencias de abastecimiento existente, era el artículo de protección al que podían dar salida más rápido, la cervecera buscó modelos preexistentes para dotar de velocidad al proceso. Usó el fin de semana para hallarlos y poder imprimir las máscaras desde el propio lunes.
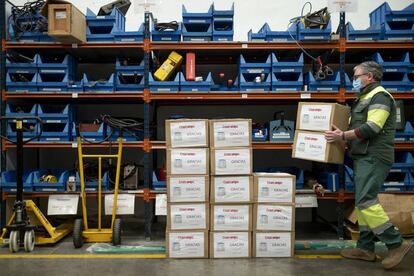
“Hacemos más de 100 pantallas diarias y ya hemos entregado más de 2.000”, explica Juan Padilla, responsable de digitalización y automatización de la fábrica de Sevilla de Cruzcampo. El personal de la factoría se ha presentado voluntario para ayudar en la tarea, para que las máquinas estén operativas a pleno rendimiento. “La gente está muy satisfecha de poder poner su granito de arena para frenar la pandemia”, asegura el director de la factoría, Juan Candau.
Con la producción de cerveza al 50%, dado que la venta para hostelería y restaurantes se ha paralizado con el cierre de los establecimientos, y sin haber acometido hasta la fecha un ERTE, la mitad de las 200 personas que trabajan en Sevilla han participado en el proyecto. “Produciremos hasta que no haya demanda o hasta que nos quedemos sin materiales”, avanza Padilla. Como la mayoría de las empresas, sufraga ella misma estos consumibles.
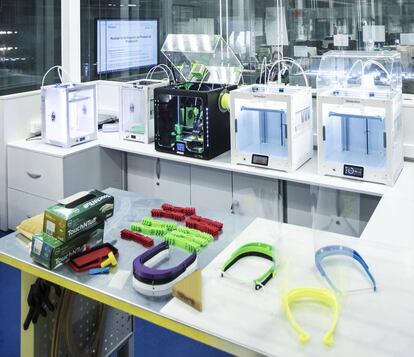
A 16 kilómetros de distancia de Cruzcampo, las instalaciones de Airbus también están trabajando en algo que nada tiene que ver con la fabricación de componentes aeronáuticos. La multinacional está utilizando sin descanso las 30 impresoras 3D que se reparten entre sus instalaciones de Sevilla, Cádiz, Madrid y Toledo para producir pantallas de protección para el personal sanitario. La factoría de Illescas es la que concentra la mayoría de los esfuerzos.
Teresa Busto, su directora, cuenta que fueron los propios empleados quienes dieron la idea de colaborar de manera altruista con los profesionales sanitarios, a la vista de la falta de equipos en los hospitales cercanos. “Nosotros teníamos plásticos e impresoras y, dada la urgencia, nos pusimos a hacer batas y viseras, primero para un par de hospitales, y ahora no damos abasto. Nos las han pedido los centros sanitarios y hospitales de Getafe, Móstoles, La Paz, el Gregorio Marañón o el Gómez Ulla de Madrid; en Ocaña, Puebla de Montalbán, Talavera de la Reina…”, desgrana la también vicepresidenta de Airbus en España.
Aunque la misión no fue fácil. “Hasta una semana después de diseñar los prototipos y probarlos no acertamos con ellos”, prosigue. Y fue cuando se decretó el permiso remunerado recuperable para las fábricas (durante la Semana Santa) cuando se lanzaron a producir a dos turnos con personal voluntario. Unas 50 personas del millar que acude cada mañana a estas instalaciones. Pese a que muchas más alzaron la mano para ayudar, “hubo colas de voluntarios para venir en sus vacaciones e incluso algunos se enfadaron por no poder hacerlo”, admite Teresa Busto.
Cogieron sus resistentes plásticos y se pusieron a hacer patrones y a cortarlos con unas máquinas gigantescas que habitualmente dividen piezas de fibra de carbono con las que se hacen los aviones. Y a unir las partes con otros ingenios selladores preparados para el mismo uso.
Hasta el cierre de este reportaje, en la planta toledana se habían confeccionado 12.200 batas protectoras para personal sanitario. Y entre todas las factorías de Airbus que participan en el proyecto entregaban 300 máscaras diarias. En ese momento, la directora de Airbus Illescas empezaba a replanificar la producción de componentes aeronáuticos para que las 11 impresoras 3D de la factoría trabajasen en el material sanitario los fines de semana y las batas protectoras solo precisasen de una o dos de sus máquinas cortadoras de fibra de carbono. Había que volver a la rutina sin abandonar su contribución para combatir la covid-19.
Sin embargo, en Pereiro de Aguiar todavía no pueden retornar a la normalidad. Las tiendas de Carolina Herrera y Purificación García permanecen cerradas. Y más de 500 de los 730 trabajadores de Textil Lonia viven un ERTE. El centenar de empleados que colaboran en el proyecto solidario busca mejoras en el confort de sus batas especiales para UCI, que pueden reutilizarse tras ser esterilizadas debido a la resistencia del material con que se fabrican, y las costureras están pendientes de que salgan de sus máquinas sin un hilo más de los precisos. Al fin y al cabo, los médicos presumen de sus protecciones firmadas por Carolina Herrera.
Allí han montado equipos polivalentes que, en función de las telas y fibras que les lleguen de los hospitales, se dedican a hacer mascarillas, batas o, desde hace poco, pijamas para los sanitarios. Este último es “un producto que requiere resistencia y durabilidad, que es justamente donde nosotros aportamos valor. Si aguanta seis u ocho lavados en lugar de cuatro es todo un triunfo”, sostienen en la compañía. De momento, cuentan con material para fabricar unos 10.000 pijamas.
“Las necesidades asustan”, aseguran los responsables de producción de Sociedad Textil Lonia, “nos llaman desde distintas comunidades autónomas y la pregunta es cuántos miles de batas podemos confeccionar la próxima semana”. No saben hasta cuándo van a seguir con sus líneas de producción alteradas para hacer esta labor. “Se está produciendo un cambio en el aprovisionamiento, ya es más abundante la oferta de equipos de protección individual, pero la gente no quiere enfrentarse al terror de la falta de abastecimiento”, explican. Porque la demanda continúa viva y porque necesitan mascarillas para sus propios empleados, la compañía textil está valorando si se lanza a producir mascarillas, batas y pijamas como actividad industrial, esta vez cobrando, y dadas las estrecheces a que se enfrenta y se va a seguir enfrentando la moda en estos tiempos de crisis provocados por el confinamiento.
El Ministerio de Sanidad considera la actividad de todas estas factorías y el resto de las que están participando solidariamente en la lucha contra la pandemia como “una herramienta indispensable para hacer frente a las necesidades sanitarias nacionales, además de un estímulo para la industria”. Así se están materializando proyectos importantes de fabricación nacional de productos sanitarios, cuyo abastecimiento anteriormente dependía mucho de la elaboración de terceros países, señalan.
Por ello no es de extrañar que aumente el número de voces, incluso dentro del propio Gobierno, que critican esa dependencia del exterior y apuestan porque las empresas españolas se encarguen de producir más material sanitario, desde medicinas hasta equipos de protección, para que la siguiente pandemia no nos coja por la espalda, con los deberes por hacer.
Entre tanto, las compañías españolas que han reconvertido sus fábricas para combatir la covid-19 y perseveran en su función de apoyo a la sociedad, esas que no quieren saber nada (aunque lo sepan) del dinero que han invertido con su respuesta de emergencia, además de sentirse orgullosas de sus equipos humanos y de su acción, creen que también han ganado. No solo porque se han demostrado a sí mismas su capacidad de adaptación a las circunstancias, como resalta Benoît Mocquant, sino porque sus plantillas se han unido más que nunca y se sienten más conectadas a la empresa. “Estos proyectos unen mucho a los empleados, se aprecia en la colaboración y en el trabajo en equipo”, sostiene Juan Candau. Quizás el compromiso también se extienda como el coronavirus después de la pandemia.—eps
Comparativas históricas
Desde una perspectiva económica, la actual debacle se parece a la Gran Depresión de hace casi un siglo, mientras que hay elementos distintos a los de la gran crisis financiera global de 2008. El reto es evitar daños estructurales para que el día que acabe el virus, la recuperación sea lo más rápida posible.
Inmersos en una nueva recesión económica, es lógico que queramos hacer comparaciones con las anteriores. Por la previsible magnitud y el impacto global de esta que acaba de empezar, las dos referencias históricas son la gran crisis financiera global (2008-2012) y la Gran Depresión (1929-1934). En estas dos, su característica común es que se tardó demasiado tiempo en reconocer que estábamos sumidos o a punto de entrar en una recesión. Esto se tradujo en que no se tomaron las medidas necesarias a tiempo y, cuando se hizo, fueron incorrectas o contrarias a lo recomendable.
En descarga de las autoridades de hace casi un siglo, debemos reconocer que entonces la capacidad de análisis de la situación era mucho más limitada. El conocimiento de cómo funcionaba la economía era notablemente inferior (el primer Premio Nobel de Economía se concedió en 1969). Además, no se habían desarrollado lo suficiente herramientas como la política fiscal (impuestos y gasto público) o la política monetaria (los bancos centrales). Se sufrió una Gran Depresión porque no se supo diagnosticar de forma correcta, porque las decisiones iniciales fueron equivocadas y porque no se contaba con herramientas suficientes para mitigar los daños.
La última gran crisis se caracterizó por su extrema complejidad. Sé que caemos en el denominado sesgo retrospectivo y que ahora las razones de aquella recesión nos parecen obvias y conocidas, pero no es así. Todo empezó en 2006 con la ralentización del mercado inmobiliario estadounidense. Luego, en verano de 2007, se trasladó a lo que parecía solo un problema de liquidez en las entidades financieras. No fue hasta un año después cuando empezaron a revelarse las debilidades de solvencia en uno de los pilares centrales de la economía mundial: el sistema crediticio. Mucho se ha publicado sobre aquellos instantes, que tuvieron como momento culminante la quiebra de Lehman Brothers, por lo que no voy a insistir. Sí recomiendo la lectura de Firefighting, el libro escrito por tres de los principales protagonistas de aquella crisis: Bernanke, Paulson y Geithner —los "bomberos", tal y como se autodenominaron (puede leerse mi reseña aquí)—. En dicha obra reconocen que nunca supieron con exactitud qué era lo que tenían que hacer ni cuál iba a ser el resultado de las medidas. Se fueron encontrando con los problemas y debían resolverlos lo antes posible, con la sensación de ir detrás, de que el "manual tradicional" no valía y de que había muchas limitaciones que superar, empezando por entender cuál era el problema. Fue una estrategia de prueba y error en una crisis en la que la ausencia de experiencia histórica hacía que afloraran críticas desde todos los lados. Por una parte, los economistas apocalípticos tenían un marco ideal para sus catastróficas profecías. Por otra estaba la opinión pública, a la que había que explicar a quién se estaba rescatando de verdad: no a los accionistas de los bancos, sino a los ciudadanos. Tenían un doble reto: hacer las cosas bien y conseguir que se entendieran y aceptaran.
Pero el área euro y, en especial, los denominados “países de la periferia” tuvimos que soportar, entre dos y tres años después, una réplica de la crisis inicial, esta vez en forma de riesgo de ruptura de la moneda común. La crisis financiera había provocado una recesión económica que derivó en una crisis de deuda pública, lo que añadía dosis de complejidad. Recuerdo con angustia aquellos momentos. Ahora nos damos cuenta de que la gravedad de aquella situación sirvió para crear las herramientas que ya utilizamos en esta (no hay mal que por bien no venga).
Durante la recesión actual se esperan caídas del PIB de hasta el 10%. Es decir, lo mismo que corrigió el PIB de España entre 2009 y 2012. Entonces la contracción se produjo en cuatro años (en Grecia fue de un 30%), mientras que ahora será en apenas seis meses. Por eso insisto en que esta recesión será más dura (por supuesto, sin contar con el drama humano de los miles de víctimas), pero no será tan compleja como la última, y este es un dato muy relevante. Desde una perspectiva económica, la actual crisis se parece mucho a la de hace casi un siglo, si bien en esta ocasión el diagnóstico se ha hecho en tiempo real y existe consenso sobre las causas y potencial desarrollo. Se trata de una crisis económica provocada por un factor que debe ser coyuntural y, por tanto, si se controla, también lo va a ser la caída del PIB. El reto es evitar daños estructurales en la economía para que el día que acabe el virus la recuperación sea lo más rápida posible. Ese reto es evitar impagos en empresas y familias. Y si el consenso en el diagnóstico ha sido un factor clave, más lo ha sido que se hayan tomado medidas contundentes y de forma rápida, sobre todo en el frente monetario. Así, los bancos centrales han reaccionado creando una enorme cantidad de dinero (del orden de cinco billones de euros) que llegará a las empresas y a las familias vía bancos, Estados y mercados financieros.
Esta es la gran diferencia respecto a la situación de 2008-2012. Entonces no había flujo de crédito ni de dinero. Los bancos eran el problema, y varios Estados y grandes empresas no tenían capacidad de financiarse. Éramos muchos los que demandábamos a los bancos centrales que tomaran medidas, pero o bien carecían de amparo legal, o bien no habían desarrollado las herramientas, o incluso existían opiniones en contra (alegando un "riesgo moral"). Ahora no es el caso. La gran crisis financiera global sirvió para que los bancos centrales desarrollaran a lo largo de un lustro la denominada política monetaria no convencional. En menos de una quincena la han vuelto a desplegar, con una intensidad y alcance muy superior a entonces. Ahora los bancos no solo no son el problema, sino que son parte de la solución para canalizar el dinero que están creando los bancos centrales. Su "potencia de fuego" (gracias a su elevada capilaridad comercial) debe centrarse en pymes y familias, muy necesitadas por cierto. Las medianas y, sobre todo, las grandes empresas deben seguir acudiendo al mercado de capitales, que no solo no debe menguar, sino crecer en estas circunstancias. Ahora no se han disparado las entonces famosas "primas por riesgo". Los Tesoros nacionales no tienen dificultades para emitir deuda pública ya que el BCE puede comprar todos los bonos que emitan. Estas diferencias con respecto a 2008-2012 pueden parecer muy técnicas, pero, créanme, son muy importantes. —EPS
David Cano es socio de la consultora Afi.
Tu suscripción se está usando en otro dispositivo
¿Quieres añadir otro usuario a tu suscripción?
Si continúas leyendo en este dispositivo, no se podrá leer en el otro.
FlechaTu suscripción se está usando en otro dispositivo y solo puedes acceder a EL PAÍS desde un dispositivo a la vez.
Si quieres compartir tu cuenta, cambia tu suscripción a la modalidad Premium, así podrás añadir otro usuario. Cada uno accederá con su propia cuenta de email, lo que os permitirá personalizar vuestra experiencia en EL PAÍS.
¿Tienes una suscripción de empresa? Accede aquí para contratar más cuentas.
En el caso de no saber quién está usando tu cuenta, te recomendamos cambiar tu contraseña aquí.
Si decides continuar compartiendo tu cuenta, este mensaje se mostrará en tu dispositivo y en el de la otra persona que está usando tu cuenta de forma indefinida, afectando a tu experiencia de lectura. Puedes consultar aquí los términos y condiciones de la suscripción digital.
Sobre la firma
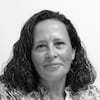