Las impresoras 3D también pueden con la cerámica
Un nuevo proceso de impresión crea estructuras de cerámica 10 veces más resistentes que los materiales disponibles en el mercado
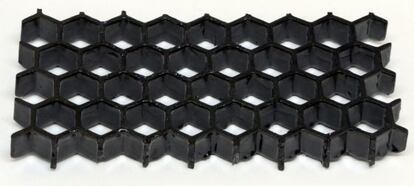
Con el calor suficiente, no hay material que se le resista a una impresora 3D. Primero fueron los plásticos y materias orgánicas blandas como el chocolate. Después le tocó el turno al acero y, más recientemente al vidrio. Pero la cerámica es otra cosa. No solo no se funde como los otros materiales, su proceso de fabricación exige una presión y temperaturas que la hacían inmune a los encantos de la impresión 3D. Sin embargo, un grupo de ingenieros ha encontrado la manera de usar una impresora comercial para conseguir estructuras cerámicas mucho más resistentes que las industriales.
La cerámica, el gres, la porcelana o los azulejos son materiales a base de arcillas (silicatos de aluminio) cuyo método de fabricación básico se remonta al Neolítico. A escala industrial, mediante un procesado denominado sinterizado, la arcilla en polvo es sometida a prensado con miles de kilos de presión por centímetro cuadrado y cocción por encima de los 1.500º. Una vez elaborada la pieza, solo materiales tan duros como el corindón o el diamante la pueden mecanizar, así que las piezas defectuosas suelen acabar en la basura.
En los años 60, el descubrimiento de polímeros (macromoléculas) de materiales cerámicos facilitó la fabricación de la cerámica pero no hasta el punto de que una impresora pueda con ella. Hay unas cuantas impresoras 3D que se han atrevido a trabajar con partículas cerámicas disueltas en resinas fotosensibles o polvos cerámicos fundibles, pero sus resultados son tan lentos de obtener, toscos, simples y frágiles que algunos pioneros como Shapeway desistieron de imprimir cerámica.
"Nuestro nuevo proceso de impresión 3D nos permite aprovechar todas las grandes propiedades de la cerámica, como si gran dureza, su resistencia, su alta refracción o su resistencia a la corrosión y la abrasión", dice Tobias Schaedler. Este científico de materiales y sus colegas de los Laboratorios HRL (EE UU) han encontrado la manera de sortear los problemas que plantea este material tan duro y frágil a la vez. "Hasta ahora, los elementos cerámicos eran muy difíciles de fabricar porque necesitan ser consolidados mediante el sinterizado de los polvos, lo que introduce el problema de la porosidad y limita tanto las formas a conseguir como la resistencia", comenta Schaedler.
El nuevo proceso usa impresoras 3D ya existentes en el mercado
Lo que ellos han hecho ha sido convertir materiales artificiales precursores de la cerámica como el siloxano o el silazano en resinas sensibles a la luz ultravioleta. Como con los modernos empastes, la resina se endurece al aplicarle luz. Los investigadores usaron una impresora 3D (una Form 1+ de Formlabs) para imprimir desde un sacacorchos hasta varias estructuras en forma de malla o panal. Para el primero, usaron una de las técnicas dominantes en la impresión 3D, la estereolitografía. Pero para las estructuras, recurrieron a un original sistema de guiado de la luz (SPPW) que iba endureciendo la resina siguiendo un patrón determinado.
"Usando la estereolitografía, se necesitan de cuatro a ocho horas para tener una estructura de cinco centímetros. Con nuestro proceso SPPW, podemos imprimir paneles de 2 cm de grosor en 60 segundos, pero la forma se limita a mallas, panales de abeja o estructuras similares", explica Schaedler.
El siguiente paso fue endurecer las impresiones mediante la cocción. Para ello usaron el procedimiento de pirólisis, horneando los materiales a 1.000º y en ausencia de oxígeno. Con ello consiguieron unas cerámicas, en particular las impresas con SPPW, de muy baja porosidad y una gran resistencia al corte y la presión. "Logramos una cerámica plenamente densa con una resistencia 10 veces mayor que la de las espumas cerámicas convencionales", asegura el científico de materiales.
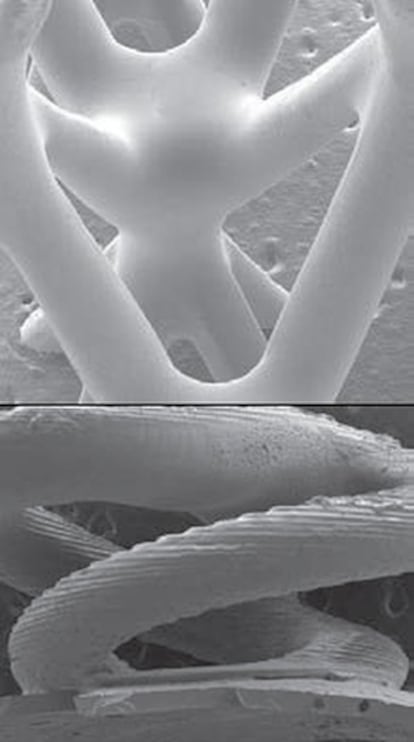
Sin embargo, la necesidad de la pirólisis aleja la impresión de cerámica del fenómeno de democratización que vive la impresión 3D, donde casi cualquiera puede imprimir ya casi cualquier cosa. "Para la pirólisis solo necesitas un horno que pueda alcanzar los 800º en una atmósfera inerte (argón o nitrógeno, no aire). Muchos artistas usan este tipo de hornos en sus estudios. Uno de esos cuesta entre 2.000 y 4.000 dólares y la impresora la compramos por unos 3.000. Así que creo que cualquiera puede hacerlo en su garaje", replica Schaedler.
En todo caso, los autores de este avance, publicado en la revista Science, dejan claro que se trata de un primer paso y que, como pasó con otros materiales, como el plástico o el acero, la impresión 3D de cerámica avanzará siguiendo sus pasos: cada vez más objetos, mayor calidad y menor coste. En el caso de las cerámicas, Schaedler, estima que aún faltan unos cinco años para que el proceso sea una realidad comercial. Para entonces, cree que no se tratará de imprimir un sacacorchos o unas cuantas baldosas para casa, sino para algo más sofisticado, "desde componentes de motores de reacción y vehículos hipersónicos a intrincadas partes de dispositivos de microelectrónica".
Tu suscripción se está usando en otro dispositivo
¿Quieres añadir otro usuario a tu suscripción?
Si continúas leyendo en este dispositivo, no se podrá leer en el otro.
FlechaTu suscripción se está usando en otro dispositivo y solo puedes acceder a EL PAÍS desde un dispositivo a la vez.
Si quieres compartir tu cuenta, cambia tu suscripción a la modalidad Premium, así podrás añadir otro usuario. Cada uno accederá con su propia cuenta de email, lo que os permitirá personalizar vuestra experiencia en EL PAÍS.
¿Tienes una suscripción de empresa? Accede aquí para contratar más cuentas.
En el caso de no saber quién está usando tu cuenta, te recomendamos cambiar tu contraseña aquí.
Si decides continuar compartiendo tu cuenta, este mensaje se mostrará en tu dispositivo y en el de la otra persona que está usando tu cuenta de forma indefinida, afectando a tu experiencia de lectura. Puedes consultar aquí los términos y condiciones de la suscripción digital.
Sobre la firma
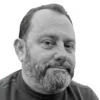