Cómo producir 100 móviles por minuto
Más de 20.000 empleados trabajan allí junto con miles de robots las 24 horas del día para producir 200.000 móviles diarios. Entramos en la planta de Oppo de Dongguan, la ciudad del noroeste de China en la que se fabrica uno de cada cinco de los ‘smartphones’ del mundo.
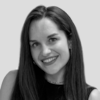
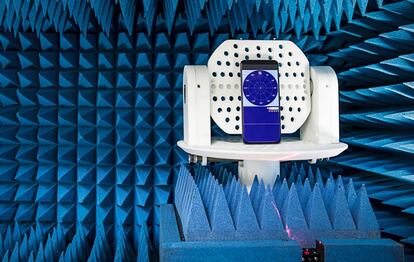
Varias máquinas sueltan smartphones desde una altura de un metro. Los móviles caen con fuerza sobre una placa de mármol. Tras el impacto, algunos trabajadores revisan si alguno se ha roto. En la mayoría de los casos, a primera vista siguen intactos. Y el proceso vuelve a empezar.
Esta es solo una de las más de 150 pruebas a las que son sometidos a diario decenas de móviles de la marca china Oppo. Tiene lugar en su fábrica en Dongguan, una ciudad de ocho millones de habitantes vecina de Shenzhen y perteneciente a la provincia suroriental de Guangdong, la capital china de la electrónica. En ella, Oppo y fabricantes como Huawei o Vivo producen uno de cada cinco de los smartphones del mundo.
O al menos eso sucedía cuando EL PAÍS Retina visitó la zona, justo antes del estallido de la crisis del coronavirus. De las líneas de producción que Huawei tiene allí salen unos 90.000 terminales diarios. “Cada día producimos los mejores móviles de todo el mundo”, reza una de las pancartas en el lugar. Más de 20.000 empleados trabajan junto a todo tipo de máquinas y robots. Se encargan desde de la colocación de la primera pieza hasta de que el smartphone esté listo para ser enviado a cualquier parte del planeta. También someten sus productos a severas pruebas de resistencia y testean el sonido, las aplicaciones, la batería o los cables de los móviles. Nada puede fallar.
Carrera contrarreloj
Más que 'smatphones'
por un dedo robótico con una presión de un kilogramo. “Si un usuario hiciera clic en los botones 50 veces al día, le llevaría alrededor de seis años realizar esas 100.000 pulsaciones”, explica una empleada de Oppo. A unos metros del departamento de calidad, se encuentran diferentes líneas de montaje. Para acceder a una de las 26 existentes hay que pasar por una especie de ducha de aire desinfectante. En el interior, decenas de ingenieros y técnicos con uniformes y gorros azules trabajan codo a codo con todo tipo de máquinas. Nada más entrar, múltiples aparatos imprimen placas base. Cada mes se producen 7,5 millones. Otras con visión óptica analizan los chips, que luego son revisados por empleados. Mano a mano con robots Este trabajo conjunto entre máquinas y humanos es común en todo el proceso. Chen apuesta por la coexistencia entre más que ‘smartphones ’ “¿Cómo interactuamos ahora con nuestro teléfono y cómo lo hacíamos hace años, cuando aún tenía teclas?”, pregunta en un evento organizado por Oppo Tom Morrod, director ejecutivo de investigación de IHS Markit. La conectividad, según sostiene, va a suponer un cambio similar en nuestra forma de interactuar con el smartphone. De ahí viene la apuesta de Oppo por crear un ecosistema de dispositivos conectados que complementen a los móviles. El fundador de Oppo, Tony Chen, considera que “no habrá ninguna compañía en la industria que se centre solo en los teléfonos inteligentes. Los móviles continuarán siendo un motor clave de nuestro ecosistema. Pero en el mundo conectado también tendremos relojes inteligentes, auriculares inalámbricos, gafas de realidad aumentada e incluso robots inteligentes”.
Cada minuto es importante. La fábrica de Oppo está en marcha 24 horas al día. Allí también tiene lugar desde la soldadura de los circuitos de la placa base hasta el control de calidad del producto terminado, pasando por el ensamblaje de los componentes. Más de 20.000 empleados trabajan sin descanso junto a miles de máquinas. Además de testear la resistencia de diferentes modelos, producen cada día 200.000 móviles. Es decir, más de 8.300 terminales por hora o de 100 por minuto. Oppo ha llegado hasta ahí en una década y media.
La compañía fue fundada en 2004, comenzó su internacionalización en 2010 y ya es el quinto mayor fabricante de móviles del mundo, por detrás de Samsung, Huawei, Apple y Xiaomi, según IDC. Solo en el tercer trimestre de 2019 vendió 31,2 millones de terminales, según datos facilitados por la compañía, especialmente exitosa en el mercado asiático. De hecho, en febrero de 2017 logró ser el fabricante de smartphones con más ventas en China tras superar, aunque por poco tiempo, al gigante Huawei. En la actualidad sigue manteniéndose en los primeros puestos del ránking de ventas de este país. Además, presume de ser líder en Indonesia y Filipinas y número dos en otros mercados asiáticos como Malasia, Tailandia y Vietnam.
Entre sus prioridades está diferenciarse por el diseño. Algunos terminales, como el Reno 2, se caracterizan por un acabado elegante y una aleta frontal que despliega la cámara para selfis. Pero a diferencia de otros gigantes tecnológicos como Samsung o Huawei, la compañía no se ha lanzado al mundo de los plegables. Alen Wu, presidente mundial de ventas de Oppo, explica que diseñan los terminales teniendo en cuenta las demandas de los usuarios. “Por el momento, no hemos encontrado el escenario adecuado para ese formato”, afirmó el pasado diciembre en un encuentro con periodistas internacionales en la sede de Oppo en la ciudad china de Shenzhen.
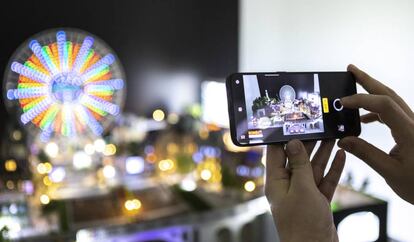
El potro de torturas del móvil
Aún así, algunos de sus terminales incorporan tecnologías novedosas. Por ejemplo, la compañía ha presentado recientemente el móvil con la carga más rápida del mundo y el primer terminal con una cámara debajo de la pantalla. Su apuesta por la innovación no acaba aquí, según el fundador y presidente de Oppo, Tony Chen. En su primer discurso público en seis años, en diciembre de 2019, anunció que la inversión en I+D de la tecnológica se multiplicará por cinco durante los próximos tres años, hasta los 6.400 millones de euros.
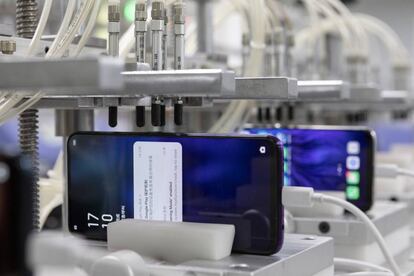
Dejar caer los móviles desde diferentes alturas y ángulos forma parte del proceso de control de calidad, el departamento en el que se somete a los dispositivos a todo tipo de torturas. Cada modelo pasa más de 150 pruebas que se dividen en tres bloques: pruebas de rendimiento eléctrico, pruebas estructurales y pruebas de envejecimiento ambiental. Al test de caídas desde altas alturas se suma el de microcaídas. Varias máquinas dejan caer el smartphone 20.000 veces desde una altura de siete centímetros. Así se simulan los golpes suaves que puede sufrir un móvil al caer con la pantalla, la trasera o los laterales. Otras máquinas analizan cómo responde el móvil a temperaturas extremas, polvo, humedad, sudor o agua.
Por ejemplo, el terminal se introduce en una cámara repleta de chorros de agua o es sometido a temperaturas de 85 grados durante 500 horas. También se ponen a prueba las teclas de volumen y de desbloqueo. Cada una es pulsada 100.000 veces por un dedo robótico con una presión de un kilogramo. “Si un usuario hiciera clic en los botones 50 veces al día, le llevaría alrededor de seis años realizar esas 100.000 pulsaciones”, explica una empleada de Oppo.
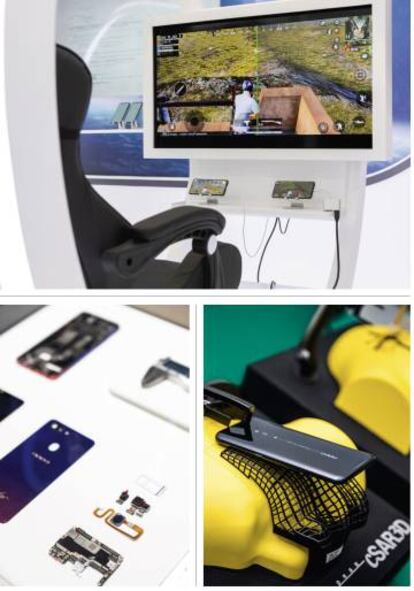
A unos metros del departamento de calidad, se encuentran diferentes líneas de montaje. Para acceder a una de las 26 existentes hay que pasar por una especie de ducha de aire desinfectante. En el interior, decenas de ingenieros y técnicos con uniformes y gorros azules trabajan codo a codo con todo tipo de máquinas. Nada más entrar, múltiples aparatos imprimen placas base. Cada mes se producen 7,5 millones. Otras con visión óptica analizan los chips, que luego son revisados por empleados.
Mano a mano con robots
Este trabajo conjunto entre máquinas y humanos es común en todo el proceso. Chen apuesta por la coexistencia entre ambos: “Las máquinas son máquinas y nunca van a reemplazar a los seres humanos”. Cada dispositivo se tarda en fabricar unas dos horas en un proceso en el que participan unas 90 personas.La compañía no ha especificado el coste de fabricar un terminal.
Mientras que diferentes brazos robóticos dan forma al Oppo Reno 2, empleados con una especie de fundas en los dedos examinan cuidadosamente lo que hacen las máquinas. Prueban la pantalla táctil y limpian cualquier partícula restante con un pequeño palo de plástico. Comprueban milimétricamente cada detalle: desde la cámara frontal hasta el sistema cuádruple de cámaras traseras, el audio, la temperatura o la conectividad.
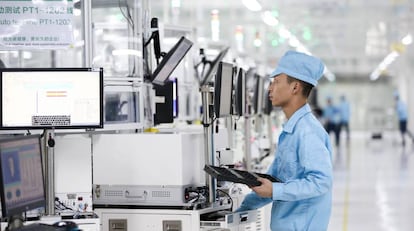
Si los móviles pasan todas las pruebas con éxito, decenas de trabajadores los esperan para la última fase. Limpian con una tela el terminal, ponen un plástico protector en la pantalla y pegan una pegatina en su parte trasera. Después, los meten en sus cajas junto a unos auriculares y un cargador. Los smartphones ya están listos para invadir las tiendas de medio mundo.
Tu suscripción se está usando en otro dispositivo
¿Quieres añadir otro usuario a tu suscripción?
Si continúas leyendo en este dispositivo, no se podrá leer en el otro.
FlechaTu suscripción se está usando en otro dispositivo y solo puedes acceder a EL PAÍS desde un dispositivo a la vez.
Si quieres compartir tu cuenta, cambia tu suscripción a la modalidad Premium, así podrás añadir otro usuario. Cada uno accederá con su propia cuenta de email, lo que os permitirá personalizar vuestra experiencia en EL PAÍS.
¿Tienes una suscripción de empresa? Accede aquí para contratar más cuentas.
En el caso de no saber quién está usando tu cuenta, te recomendamos cambiar tu contraseña aquí.
Si decides continuar compartiendo tu cuenta, este mensaje se mostrará en tu dispositivo y en el de la otra persona que está usando tu cuenta de forma indefinida, afectando a tu experiencia de lectura. Puedes consultar aquí los términos y condiciones de la suscripción digital.
Sobre la firma
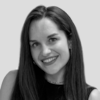