El botón de hacer coches
La tecnología 3D permite a los fabricantes aligerar pesos, acortar plazos y abaratar costes. En 2019 podrá comprar el primer vehículo salido íntegramente de la impresora.

El coche estará listo en tres días, pesará solo 450 kilos y se podrá comprar, recién hecho, por unos 8.000 euros. Se trata de un pequeño automóvil eléctrico de poliuretano termoplástico (TPU) que se llamará LSEV, medirá menos de 2,5 metros y ofrecerá 149 kilómetros de autonomía. Ocurrirá en 2019, el año que viene. De las cifras anteriores la más espectacular es la primera (tres días), y todo gracias a las ventajas que aporta la tecnología de impresión 3D. Este es probablemente el proyecto más llamativo de cuantos se desarrollan en este terreno, pero ni mucho menos el único.

Las marcas generalistas (y algunas exclusivas) se apuntan a la fabricación aditiva —el añadido de capas de material para crear un volumen— porque aligera las piezas, acelera los procesos y abarata los costes. Un caso bien aparente es el de Bugatti, que ha ensayado esta técnica con los frenos del impresionante Chiron, el supercoche de los 1.500 CV y el astronómico precio de 2,4 millones de euros. La marca italiana ha conseguido una pinza de freno de titanio después de emplear 2.213 capas del material, derretido por los cuatro láseres del Laser Zentrum Nord (Hamburgo, Alemania). No deja de ser una prueba, pero indica el camino que puede seguir la industria.
Por ejemplo, la impresión 3D puede ofrecer alternativas muy interesantes en el intrincado mundo de las piezas de recambio, especialmente en modelos antiguos (con los proveedores fuera de juego), pero el camino es largo. Así lo están comprobando en Volkswagen Classic Parts, donde probaron a clonar una pieza de la manivela de la ventanilla de un viejo Volkswagen Corrado. “El fino estriado interno y externo del engranaje requerían un alto nivel de precisión. Una simple clonación de una pieza de recambio no es aún posible, desafortunadamente”, reconoce uno de los responsables de este departamento de la marca alemana, Tobias Pape.
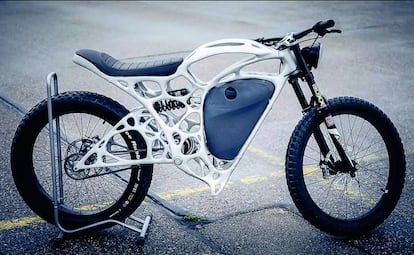
Partiendo de cero parece más fácil cumplir los objetivos. Lo demuestran el propio LSEV, que se construye con 57 piezas (frente a las 2.000 de un coche normal), o el soporte de asiento fabricado por General Motors gracias al acuerdo de colaboración con Autodesk, el gigante de software de diseño 2D y 3D. Antes era necesario crear y unir ocho piezas diferentes; ahora la pieza se genera en el ordenador y se imprime de una vez, y además resulta un 40 % más ligera y un 20 % más resistente. La consecuencia directa serán vehículos más eficientes. También Mercedes se apunta a la inercia y ya imprime (desde el año pasado) la cobertura metálica del termostato de sus camiones.
Queda claro que no se trata de rarezas de startups ni de prototipos curiosos como los estadounidenses Strati o Urbee. BMW anunció en abril una inversión de 10 millones de euros para la creación de un campus de 6.000 metros cuadrados dedicado a esta tecnología. Empezarán a producir piezas en 2019, el año de la impresión 3D.
Tu suscripción se está usando en otro dispositivo
¿Quieres añadir otro usuario a tu suscripción?
Si continúas leyendo en este dispositivo, no se podrá leer en el otro.
FlechaTu suscripción se está usando en otro dispositivo y solo puedes acceder a EL PAÍS desde un dispositivo a la vez.
Si quieres compartir tu cuenta, cambia tu suscripción a la modalidad Premium, así podrás añadir otro usuario. Cada uno accederá con su propia cuenta de email, lo que os permitirá personalizar vuestra experiencia en EL PAÍS.
¿Tienes una suscripción de empresa? Accede aquí para contratar más cuentas.
En el caso de no saber quién está usando tu cuenta, te recomendamos cambiar tu contraseña aquí.
Si decides continuar compartiendo tu cuenta, este mensaje se mostrará en tu dispositivo y en el de la otra persona que está usando tu cuenta de forma indefinida, afectando a tu experiencia de lectura. Puedes consultar aquí los términos y condiciones de la suscripción digital.