La fábrica en la que los robots bailan
Visitamos la fábrica de Volkswagen en Navarra, donde artilugios enormes de movimientos perfectos se mueven a un ritmo imperturbable y saben, sin posibilidad de error, qué paso deben dar en cada momento
En un recinto de 30.000 m2 operan no más de un centenar de personas: el 92% de los procesos está automatizado en la nave de chapistería, el territorio de unos grandes brazos articulados de color naranja. La danza resulta fluida y exquisita. Esto es El Rey León industrial y no parece extraño que haya música de fondo en el pabellón. Altos techos, luz limpia, pedazos de metal volteados en el aire. Coreografía. Da pudor preguntar cómo se titula la obra que está sonando y llenando el ambiente. Entretanto, y constantemente, llegan de la prensa las piezas de acero y van entrando en la línea de soldadura. Aquí empieza el virtuoso ajetreo de los robots.
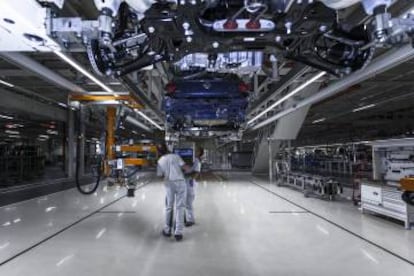
En la planta del polígono de Landaben, en Pamplona, todo se sabe desde el principio: una de las claves de la digitalización del proceso, fundamental en la industria 4.0, se esconde en el chasis del futuro vehículo, en el hueco donde después irá la rueda trasera derecha. Una etiqueta con un código de barras (se llama RFID) resume el ADN del modelo. “En esa pegatina blanca está toda la información: si el coche es de tres o de cinco puertas, si el motor es uno u otro, el tipo de tapicería… En cada módulo de trabajo una antena lee la etiqueta y los robots saben al instante qué vehículo están fabricando, de modo que pueden elegir el programa concreto. A esa etiqueta, además, podemos añadirle información, así que indicará en todo momento en qué punto de la fabricación está el coche”, resume el gerente de Chapistería, Juan Fernández.
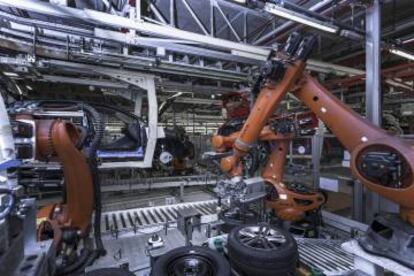
Los brazos automáticos continúan en marcha y en la nave sigue la sinfonía, que en realidad no tiene título: simplemente se oyen ruidos metálicos, ventiladores, algún chispazo ocasional, el delicado silbido de 861 robots en movimiento. Todo en orden: 235 kilos de chapa van tomando forma de carrocería.
“La industria 4.0 requiere un cambio de concepto. La tecnología existe, pero es imprescindible la creatividad para aplicarla al día a día. Esa es nuestra tarea: inventar la manera de hacer realidad un producto. Y el objetivo es que la fabricación sea autónoma y flexible, que se autoajuste. Para eso hace falta una conectividad completa y cerrada, que en logística [los encargados de proveer de materiales a la fábrica], por ejemplo, estén conectados con cada uno de los robots de chapistería”, explica el director de Ingeniería de Planificación de la planta navarra, José Arreche, que repite a conciencia y varias veces tres palabras: autoorganización, conectividad y automatización. Mientras tanto, ahí al lado, los robots van a lo suyo.
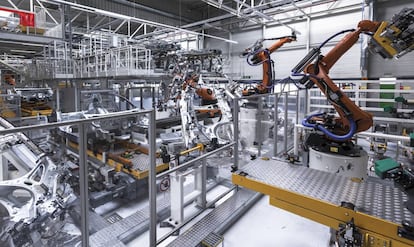
"El camino hacia la automatización implica que esta haya llegado también al transporte y suministro de materiales a pie de línea”. Traducido: cerca de 60 máquinas tractoras de diversos tamaños se mueven solas por varios pabellones de la planta mediante un sistema de filoguiado. Una banda magnética incrustada en el suelo marca la ruta, en la que las FTS (así las llaman de manera genérica, del alemán ‘Fahrerlos Transport System’) van leyendo etiquetas —de nuevo la conectividad— para tomar las decisiones oportunas: acelerar, frenar, girar en un cruce, recoger un contenedor, abandonar otro… No hay riesgo de atropello para los trabajadores ni para los visitantes ocasionales.“Lo más importante de este sistema es la seguridad. Un láser inferior y otro superior detectan los obstáculos y detienen la máquina al instante si es necesario”, anticipa Santiago Herrero, gerente de logística. Y es cierto: el frenado de emergencia funciona.
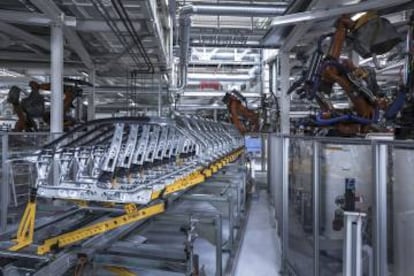
Al cabo del día, las FTS, que también pueden usarse con conductor, hacen 1.338 viajes en modo automático y recorren 446 kilómetros, especialmente en la zona de montaje. Pero no hay prisa por llegar allí. El esqueleto de acero, la carrocería desnuda, entra antes en un periodo de extraño sosiego al dejar chapistería; se da un baño de pintura, pasa por el horno de secado y vestida ya con su traje de color definitivo llega al túnel de luz, el lugar más deslumbrante de la fábrica. Lo es en un sentido doblemente literal, porque ofusca la vista y causa admiración a partes iguales.
La nave está oscura y en silencio, sin trabajadores, solo con las carrocerías que van llegando al túnel y se detienen en él durante 18 segundos. Y de pronto la luz. Unos 270.000 diodos led iluminan la escena y 30 cámaras de fotos toman 15 imágenes por segundo de la carrocería, alrededor de 8.100 en total. Un ordenador se ocupa de analizarlas y de encontrar defectos a partir de 0,2 mm de diámetro, y de enviar la información una planta más abajo, donde varios trabajadores resuelven manualmente los errores detectados. “La tecnología la creó la Universidad Politécnica de Valencia y en ninguna fábrica del mundo se utiliza con tal grado de precisión como aquí”, sostiene el Gerente de Pintura, Francisco Rodríguez.
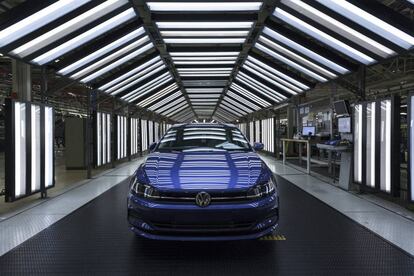
La quietud del túnel de luz no deja de ser un equívoco paréntesis en el proceso. Mientras leía el párrafo anterior, de la línea de montaje de Pamplona ha salido un nuevo Polo. Para que las cuentas cuadren, claro, póngase en el caso de que ha invertido 54 segundos exactos en descifrar esas nueve frases. Si por un casual se le ocurre comprobarlo y cronometrar la lectura (no hay motivo, de verdad), habrá otro Polo en suelo navarro, y así durante 24 horas al día, siete días a la semana, 365 días, etcétera, salvo durante las pausas marcadas por el convenio laboral. 1.408 coches al día. Un contador digital al final de la línea señala el avance implacable de los números. La nave con más vida de Volkswagen Navarra es en realidad esta, la de montaje, donde se concentran la mayoría de los empleados en tres turnos laborales. Aunque en las fábricas digitalizadas el peso lo llevan las máquinas, el cerebro y las manos humanas son fundamentales.
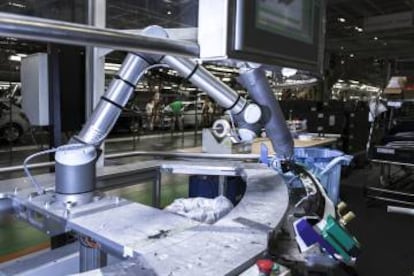
A un ritmo casi tan imperturbable como el de los robots, las manos expertas colocan los asientos, el volante, las luces, la carátula central… También con muy poca probabilidad de error y sin que la cadena se detenga. El Internet de las Cosas facilita la vida de los empleados. Cada vez que pasa un coche por un punto concreto de la línea, 54 segundos, el operario no consulta una etiqueta en papel o un denso catálogo para elegir la pieza oportuna, ni siquiera mira una pantalla.
El director de Ingeniería de Planificación, José Arreche, explica el funcionamiento del sistema de estanterías inteligentes Pick to Car: “El coche se comunica automáticamente con el mueble que guarda las piezas en orden y la etiqueta RFID manda el mensaje: soy el coche 827531 del cliente X, y este cliente ha pedido un volante deportivo de cuero. Una lucecita se enciende en la estantería y el operario coge la pieza adecuada. Así evitamos el posible fallo de poner un volante que no tocaba y además podemos ofrecer más flexibilidad al cliente sin complicarnos la vida nosotros”.

Existen 28 variantes de volante, 26 parasoles diferentes o 24 tubos de aire acondicionado distinto, 26 tipos de pomos... En Logística ponen cordura a este aluvión de números (son miles de combinaciones posibles para cada Polo) mediante la secuenciación: con un lector de códigos Bidi en una mano y una PDA en la otra los trabajadores se aseguran al instante de que están completando bien las estanterías que irán después a pie de línea. Si las piezas no llegaran clasificadas y ordenadas en función del flujo de coches, los trabajadores de la cadena de montaje se volverían locos.
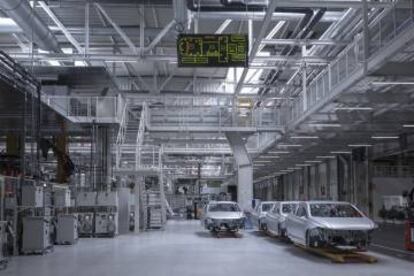
“La fábrica está completamente automatizada, salvo en Montaje. Todavía es una línea tradicional, pero vamos metiendo alguna automatización: el Farber, las ruedas, el robot colaborativo”, anticipa José Arreche.
Uno de los momentos más entrañable para los responsables de la fábrica es el de la boda, una cada 54 segundos. El módulo de trabajo llamado Farber une automática y definitivamente la carrocería con el chasis, ya con el motor acoplado. El gerente de Montaje, Víctor Irízar, explica la operación con cierto arrobo, quizá por la seguridad de que no habrá divorcio. Pero vista desde fuera, quizá sin comprender la profundidad tecnológica del asunto, la ceremonia resulta algo fría.
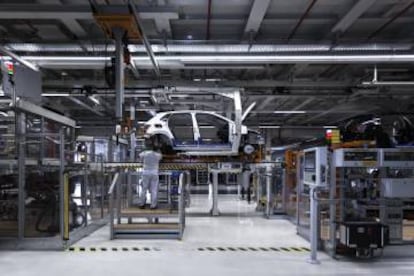
Es mucho más emocionante lo que ocurre un poco después con las ruedas, pura filigrana en el aire de seis robots en danza, tres a cada lado de la línea. Uno de ellos toma una fotografía en 2D de la rueda para determinar la posición de los agujeros de los tornillos (que varía en función del tamaño de la llanta), el segundo levanta la rueda y espera a que el tercero haga una foto en 3D de la carrocería, necesaria para que el brazo que sujeta el neumático lo coloque exactamente en su lugar. Entretanto, el primero de los robots ya está listo para atornillar. La precisión es milimétrica, la interacción es tan natural como si se conocieran de toda la vida. El trabajo en común entre máquinas y personas será el siguiente paso. De momento no pueden compartir espacio por cuestiones de seguridad: en cuanto un robot autónomo detecta a un operario, se detiene.
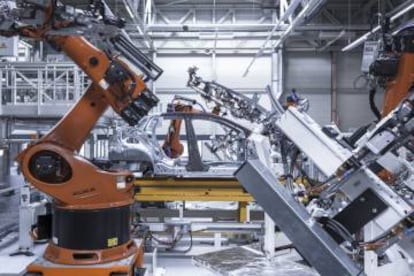
En Landaben solo hay una excepción: el robot colaborativo, casi al final de la cadena, un pequeño brazo encargado de poner la masilla que une el alerón del Polo GTI a la carrocería. Su misión es distribuir el hilo de pegamento con exactitud, la misma cantidad siempre, para que el operario coja el alerón y lo coloque. Puede parecer una tarea menor, pero supone un paso gigantesco. “Venimos de la vieja escuela y nos cuesta asumir que un robot pueda trabajar con nosotros, este ejemplo nos ayuda a pensar que son seguros y que trabajan bien. El objetivo es eliminar las tareas que pueden ser más penosas para la gente, por repetitividad o ergonomía”, detalla Arreche. Es el esbozo de la quinta revolución industrial, todavía lejana: queda mucho para que los robots sepan hacer coches por sí solos.
Tu suscripción se está usando en otro dispositivo
¿Quieres añadir otro usuario a tu suscripción?
Si continúas leyendo en este dispositivo, no se podrá leer en el otro.
FlechaTu suscripción se está usando en otro dispositivo y solo puedes acceder a EL PAÍS desde un dispositivo a la vez.
Si quieres compartir tu cuenta, cambia tu suscripción a la modalidad Premium, así podrás añadir otro usuario. Cada uno accederá con su propia cuenta de email, lo que os permitirá personalizar vuestra experiencia en EL PAÍS.
En el caso de no saber quién está usando tu cuenta, te recomendamos cambiar tu contraseña aquí.
Si decides continuar compartiendo tu cuenta, este mensaje se mostrará en tu dispositivo y en el de la otra persona que está usando tu cuenta de forma indefinida, afectando a tu experiencia de lectura. Puedes consultar aquí los términos y condiciones de la suscripción digital.