Los nuevos aviones se ‘imprimirán’ en 3D
Airbus explora innovaciones pequeñas y grandes para optimizar la fabricación de aeronaves y su explotación
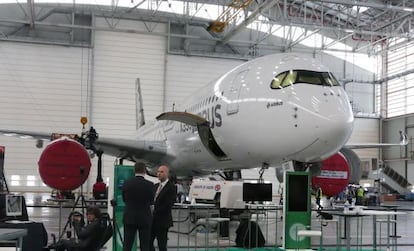
Desde unas alas hechas de materiales deformables que adquieren la forma aerodinámica óptima en distintas fases del vuelo hasta unas simples bridas hechas de papel para sujetar cables que facilitan su instalación, piezas de aviones susceptibles de ser fabricadas con tecnología de impresión 3D o un sistema electrónico que verifica si todos los cinturones de seguridad de los pasajeros están abrochados, múltiples tecnologías emergen en la industria aeronáutica. No todo son grandes proyectos de I+D para aligerar la estructura de las aeronaves o reducir el consumo de los motores. Airbus, un consorcio que invierte 3.400 millones de euros al año (en 2014) en investigación y desarrollo, también busca y promociona un sinfín de trabajos de innovación de pequeña escala que probablemente acaben incorporados a los aviones y que pueden acaba exportándose a otros sectores industriales. Recientemente la compañía ha presentado varios desarrollos de mayor o menor complejidad, pero todos potencialmente aplicables a corto o medio plazo, en una jornada dedicada a la innovación aeronáutica y celebrada en sus instalaciones de Toulouse (Francia). Estas son algunas de esas innovaciones:
Impresión 3D para piezas de avión
“Un avión A350 XWB tiene unos seis millones y medio de piezas y hemos identificado hasta el momento unas 6.500 que pueden ser fabricadas ya con tecnología de impresión 3D”, explica Sten Gatzke. Su proyecto consiste en un sistema basado en escáner 3D que identifica partes del avión que son susceptibles de ser fabricadas con esta tecnología que va depositando capas de material pulverizado hasta completar la pieza, sin cortes, sin moldes, sin desperdicio de metal, plástico, etcétera. “Buscamos identificar piezas con formas y propiedades determinadas, de un material idóneo, en las que es ventajoso aplicar esta técnica”, continúa Gatzke, mostrando a modo de ejemplo un tubo de titanio con que lleva en el interior varios conductos, un tipo de pieza muy difícil de hacer con un molde. Los herrajes que sujetan el guarnecido de la pared interior del fuselaje del avión son piezas adecuadas, o los apoyabrazos de plástico de los asientos, la sujeción de los cinturones… La base de datos que se está elaborando para identificar todas las partes de un avión adecuadas para la producción con esta técnica, que aporta reducción de costes y tiempo de fabricación, se está utilizando desde el pasado verano en su primera versión.
Por muy revolucionaria que sea la impresión 3D, tiene aún limitaciones, por ejemplo de tamaño de la pieza. “Hasta ahora, el límite en la industria está en piezas de 64x41x53 centímetros”, explica Gatzke, pero dice que la tecnología está avanzando rápidamente y que en el futuro, probablemente, se superarán esas dimensiones.
El 'Internet de los objetos'
La verificación de los chalecos salvavidas colocados bajo cada asiento (si todos lo tienen y si cada chaleco ha pasado la revisión legal en su fecha), o la comprobación de que todos los pasajeros llevan abrochado el cinturón antes de despegar, no necesitarán dentro de poco un recuento manual o una verificación visual si se instala en las aeronaves el sistema denominado Internet de los objetos, actualmente en desarrollo. “Para crear un entorno inteligente necesitas objetos inteligentes”, comenta Trevor Stone en su zona de demostración dentro del hangar donde Airbus presenta una selección de sus innovaciones.
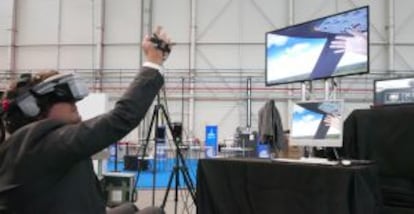
La idea es dotar a innumerables objetos de las aeronaves de etiquetas de identificación con de emisores de radiofrecuencias para tener así un seguimiento completo y en tiempo real de ellos en cada momento. Un sistema de antenas hechas de aluminio embebido en las paredes del avión configuran esta red, “y no, no interfiere en los sistemas del avión”, recalca Stone. Es una infraestructura de software y hardware que permitirá evitar procesos manuales y errores humanos en las verificaciones. El sistema ya funciona para componentes del avión (hasta 3000 cosas van identificadas ya en una aeronave de última generación), pero ahora se trata de extenderlo a la cabina de pasajeros y, en un par de años, puede estar listo, añade el experto. Por supuesto, el sistema es aplicable eficazmente a la carga así como a cada pieza de equipaje de los pasajeros, que estará perfectamente localizada en cada momento.
Bridas de papel para sujetar cables
A Maud Didnee le bastan unos manojos de cables, unas bridas de plástico, unas pequeñas tijeras y unas tiras de papel para explicar su innovación: precisamente son esas bridas de papel rojo la solución sencillísima que propone para un problema habitual en el proceso de montaje que se hace patente cuando ella lo explica. Muchos cables de los aviones, y son kilómetros en cada aparato, van agrupados y sujetos con bridas a lo largo de conductos o superficies y hay que irlos separando en los puntos de destino de cada uno, por ejemplo la luz en cada asiento; el problema es que esos cables llegan al montador unidos por bridas de plástico (unas 800.000 al año se usan en los talleres de los A350 XWB solo en el Reino Unido, señala Didnee) que tiene que ir cortando con unas tijeras para separarlos, y el corte supone un serio peligro para los finos hilos eléctricos (un cable dañado no es reparable y hay que reemplazarlo entero, con el coste que ello conlleva). La solución podrían ser esas nuevas bridas de papel que sujetan bien los cables y que se cortan fácilmente tirando de ellas con la mano, sin tijeras. Tan sencillo y tan eficaz. Además, las bridas se hacen de papel reciclado en lugar de nailon, con la consiguiente ventaja añadida de ser “ecológicas”. El invento, ya patentado, está en fase de pruebas, señala Didnee durante la visita (patrocinada por Airbus) a la muestra de innovaciones.
Compactador de residuos a bordo
Un carrito parecido a los que usa la tripulación a bordo de un avión para recoger toda la basura que genera el pasaje y el servicio esconde una novedad: es, a la vez, un compactador capaz de reducir a la mitad su volumen de desperdicios. La solución está en un sistema de vació similar al que se utiliza en los aseos de a bordo. El carrito, en realidad mide la mitad que uno normal, tiene una bolsa especial de basura y un interfaz de vació que, una vez recogidos los papeles, los restos de las bandejas de comida, los plásticos, etcétera, se acopla a un dispositivo instalado en la zona de servicio y extrae el aire, reduciendo el volumen de los residuos y facilitando su almacenaje en el avión, explica Nicolas Jourdan. Se va a ensayar el año que viene en el centro de integración y pruebas de vuelo en Hamburgo.
Materiales inteligentes
Piet-Christof Woelcken y sus colegas exploran el mundo de los nuevos materiales para aplicarlos en lo que denominan “estructuras inteligentes para aviones”. Se trata de utilizar materiales con propiedades mecánicas y eléctricas mejoradas mediante la nanotecnología, añade. Una pieza, por ejemplo, puede así “decirte si está dañada o no, si puede reutilizarse o no…”. Sobre un banco de trabajo tiene una sección del borde de ataque del ala de un avión que se deforma, con unos actuadores internos, como si fuera una lámina de plástico flexible. Así adquirir la geometría aerodinámica óptima del ala, la más eficiente. Y al tocarlo, el material casi quema: “Es para fundir el hielo que se forme en las alas”, explica Woelcken, que dirige este proyecto de 51 millones de euros (32 de la Comisión Europea), para cuatro años, en el que participan más de mil expertos de universidades, empresas e instituciones de investigación.
Un programa va indicando al trabajador en unas gafas inteligentes las operaciones a realizar en una fase de montaje
También se pueden integrar en la estructura del avión sistemas de protección ante los rayos o sensores que aumentan la seguridad del aparato al tiempo que reducen el coste de revisión y mantenimiento. Además, las estructuras multifuncionales, señalan los investigadores, pueden suponer una reducción de peso de la aeronave entre 80 y 500 kilogramos, mientras que las superficies deformables en las alas, que reducen las turbulencias y vibraciones proporcionando un control preciso de la sustentación y la resistencia aerodinámica, reduce el consumo de combustible. Son tecnologías en desarrollo con vistas a convertirse en realidad en la próxima década.
Realidad virtual para probar la cabina
Los costosos y complejos simuladores de vuelo que se utilizan en el desarrollo de un nuevo avión, así como los utilizados en el entrenamiento de pilotos o determinados ensayos de aviones no van a desaparecer con la cabina traducida a realidad virtual que presentan Daniel Dreyer y sus colegas. Pero hay fases de desarrollo de nuevas aeronaves en las que no se precisa tanto detalle, incluso físico, que ofrecen esos simuladores avanzados. Y la nueva herramienta que va presentando en pantallas las condiciones de vuelo y la instrumentación, con el piloto embutido en guantes, casco y gafas de realidad virtual, aspira a ser una alternativa barata y funcional “en las primeras fases de diseño”, asegura Dreyer.
El sistema, que se está ya utilizando en el Grupo Airbus, es flexible, puede adquirir diferentes configuraciones reproduciendo la geometría de la cabina en las diferentes pantallas y “resulta muy realista en condiciones de vuelo”, continúa. Es como un “borrador previo de simulador de vuelo”. También se reduciría el tiempo y los costes de entrenamiento de los pilotos ya que utilizarían estos simuladores virtuales de familiarización antes de pasar a los simuladores reales.
Gafas para los trabajadores
Una pequeña pantalla ante un ojo y sujeta a la cabeza, con el debido programa, puede suponer una gran ayuda para los trabajadores que se ocupan de montaje de aviones, o del acabado de las cabinas. Delante del ojo puede aparecer, por ejemplo, la plantilla de una puerta de avión que indica donde van exactamente pegados los carteles de avisos o de indicaciones de dispositivos; la plantilla se sobrepone a la visión real del objeto que ve el operario y este solo tienen que ir pegando los adhesivos que se proyectan ante él. Basta con que antes de esta labor concreta, escanee un código de barras específico que carga la ficha de barras correspondiente en las gafas inteligentes.
Un avión A350 XWB tiene unos seis millones y medio de piezas y hemos identificado hasta el momento unas 6.500 que pueden ser fabricadas ya con tecnología de impresión 3D”
Más complicado pero igualmente eficaz es otro programa que va indicando al trabajador en las gafas inteligentes las operaciones a realizar en una fase de montaje: dónde hacer exactamente unas perforaciones concretas en una pieza, con qué ángulo, con qué presión trabajar, par de apriete, etcétera. Además, el sistema alerta de fallos. “Esto mejora la calidad del trabajo, es rápido y reduce tanto los fallos como el entrenamiento necesario para la labor”, explica Stephane Ripoll.
`App´ para los empleados de viaje
En un grupo empresarial gigante como Airbus, miles de sus empleados están viajando constantemente a las diferentes plantas de fabricación repartidos por toda Europa (además de China y EE. UU.), los centros de diseño y de investigación, visitando clientes en todo el mundo…. “Aproximadamente un tercio de la plantilla son viajeros frecuentes, es decir, que viajan más de cinco veces cada año”, afirma Xavier De-Larboust.
Para facilitarles la vida en esos desplazamientos, se ha diseñado una aplicación para ordenadores y dispositivos móviles (teléfonos y tabletas), que permite localizar a empleados de la empresa que estén en cada momento en un lugar concreto, se dirijan hacia allí o hayan estado y puedan aportar datos interesantes sobre transporte, restaurantes, hoteles, etcétera. Compartir información con colegas, o un vehículo para desplazarse en una zona donde puedan estar otras personas de Airbus, quedar a cenar o pasar y recabar datos de viaje y sugerencias, debe ser sencillo con esta aplicación, cuyo “uso es absolutamente voluntario”, recalca De-Larboust, y que está en fase piloto.
Tu suscripción se está usando en otro dispositivo
¿Quieres añadir otro usuario a tu suscripción?
Si continúas leyendo en este dispositivo, no se podrá leer en el otro.
FlechaTu suscripción se está usando en otro dispositivo y solo puedes acceder a EL PAÍS desde un dispositivo a la vez.
Si quieres compartir tu cuenta, cambia tu suscripción a la modalidad Premium, así podrás añadir otro usuario. Cada uno accederá con su propia cuenta de email, lo que os permitirá personalizar vuestra experiencia en EL PAÍS.
En el caso de no saber quién está usando tu cuenta, te recomendamos cambiar tu contraseña aquí.
Si decides continuar compartiendo tu cuenta, este mensaje se mostrará en tu dispositivo y en el de la otra persona que está usando tu cuenta de forma indefinida, afectando a tu experiencia de lectura. Puedes consultar aquí los términos y condiciones de la suscripción digital.