Ensayo del coche del futuro
Renault pone en marcha un proyecto piloto de digitalización de sus fábricas en Valladolid, Cleon y Curitiba para producir el vehículo conectado, eléctrico y autónomo
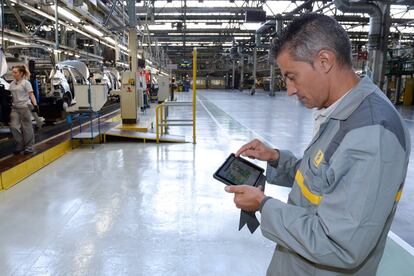
Un coche que se conduzca solo, que esté permanentemente conectado a nuestra vida digital con garantías y seguridad, que no contamine ni haga ruido. Un automóvil del que ni siquiera tengamos la propiedad, sino que sepa a dónde tiene que ir a recoger a un pasajero y a otro (o más) con el que compartirá viaje y cómo hacer la ruta más óptima para todos. Las automovilísticas están presentando en los Salones del Automóvil todas sus estrategias para las próximas décadas, planes que van más allá de tener un vehículo que corra más, sino que dan la vuelta a lo que hemos conocido como industria del motor. Y no basta con dibujarlo. Para que sea realidad, hay que fabricarlo en serie y a un coste asequible.
En este afán, Renault ha presentado su estrategia en estas dos vertientes. Por un lado, desveló su prototipo Symbioz en el reciente Salón del Automóvil de Fráncfort, y por otro, ha lanzado un proyecto piloto de digitalización de sus fábricas que se ensaya, de momento, en Valladolid, en Cleon (Francia) y en Curitiba (Brasil) con vistas a tener plataformas de producción y profesionales formados para ir encajando poco a poco los nuevos vehículos. Es la primera experiencia de la compañía automovilística en la llamada industria 4.0, la que supone la integración total de la tecnología en los procesos productivos. Son solo tres fábricas de las 36 instalaciones con las que la automovilística francesa cuenta en todo el mundo.
Principales novedades
- Inteligencia artificial. Las gafas de monitorización permiten a los ingenieros seguir desde el ordenador la vista del experto en su labor de montaje para detectar fallos, solucionarlos, y mejorar la eficiencia.
- Robots. Renault cuenta con más de 5.000 robots que realizan tareas junto a los trabajadores, como quitar tapones y preparar los kits de piezas para cada puesto. Eliminarán más tareas repetitivas o pesadas.
- Full Track & Trace. La conectividad permite garantizar la trazabilidad desde el origen hasta la entrega al cliente para todas las piezas. Renault trabaja con su red de proveedores para que garantice los datos de cada producto.
- Vehículos sin conductor. Los carros filoguiados trasladan de manera autónoma herramientas y kits de piezas a los trabajadores en los distintos puntos de la fábrica. Los pasillos son amplios y despejados para que circulen con fluidez.
“El sector del automóvil atraviesa una etapa de grandes cambios normativos y también tecnológicos. El futuro de la industria es el vehículo eléctrico, conectado, personalizado y autónomo”, explica José Vicente de los Mozos, vicepresidente ejecutivo de Fabricación y Logística del grupo Renault y máximo responsable de la Alianza Renault Nissan en España. “Symbioz es un ejemplo. Explica nuestra visión del futuro del vehículo y la fabricación tiene que adecuarse ya a los procesos tecnológicos para el mañana”, asegura.
El prototipo que sirve como guía y visión para Renault tiene mucho más de estancia y menos de coche tradicional. Es efectivamente eléctrico, tecnología por la que la Alianza Renault Nissan ha apostado con fuerza desde hace años (el Renault Zoe y el Nissan Leaf son los eléctricos más vendidos en el mundo). Será totalmente autónomo y sus asientos se distribuirán por el habitáculo como si formaran un salón cuando el conductor decida no pilotar. Pero podrá hacerlo y la configuración interior se organizará de nuevo, sacando el volante, el cuadro de mandos y los pedales. Y además, contará con una conectividad permanente con los datos y la vida digital del usuario, que podrá acceder en cualquier momento a agenda, correos electrónicos, redes sociales y documentos alojados en la nube.
La conectividad de los sistemas salta del vehículo y vertebra además la estrategia de digitalización de las fábricas porque “facilita la producción al conectar a las personas con los procesos y los productos, desde el momento del pedido al de la entrega. El objetivo es acelerar el rendimiento de nuestras factorías y garantizar la completa trazabilidad de los productos”, comenta Eric Marchiol, vicepresidente de transformación digital en fabricación y cadena de suministro del grupo Renault. Para empezar, una cosa obvia pero no tan sencilla: llevar el wifi a las factorías. Así “conectamos empleados, jefes, departamentos, pero también máquinas y robots”, explica Marchiol. “La digitalización mejora la toma de decisiones relacionada con la producción y permite la gestión de los procesos en tiempo real”, apunta De los Mozos. En la línea de montaje, los jefes de equipo cuentan con una tableta desde la que gestionan en tiempo real cuestiones que afectan tanto a sus subordinados (bajas, libranzas, turnos) como a las máquinas bajo su línea de producción o a cuestiones de suministros o calidad. “Es una revolución en la firma. Esta herramienta elimina papeles, procesos y desplazamientos y supone un ahorro de tiempo de una hora y media diaria, que se puede dedicar a otras labores”, cuenta Rafael Vázquez, responsable de la planta de Valladolid.
Industria completa
“España es el segundo país con mayor implantación del grupo Renault. Además, Valladolid es una instalación industrial muy completa porque aúna la fabricación de motores con el ensamblaje de vehículos”, explicó De los Mozos para justificar la participación de esta factoría en el proyecto mundial. La planta fabricó el año pasado 245.771 unidades del Renault Captur y unas 4.500 del cuadriciclo eléctrico Twizy.
Estos sistemas conectados permiten además el mantenimiento predictivo de las máquinas, de modo que puedan anticiparse a las averías y actuar sobre ellas antes de que tengan un efecto en la línea de producción. “Evitamos las paradas intempestivas y el deterioro de las máquinas”, explica Vázquez. La fábrica cuenta con alrededor de 1.000 robots colaborativos en distintas fases de la producción de coches y de motores, que también han de estar conectados. “Ahora mismo participan en las labores de menor valor añadido del proceso de fabricación, como quitando tapones en las piezas o plásticos. Poco a poco, ayudarán más a los empleados”, cuenta.
Tu suscripción se está usando en otro dispositivo
¿Quieres añadir otro usuario a tu suscripción?
Si continúas leyendo en este dispositivo, no se podrá leer en el otro.
FlechaTu suscripción se está usando en otro dispositivo y solo puedes acceder a EL PAÍS desde un dispositivo a la vez.
Si quieres compartir tu cuenta, cambia tu suscripción a la modalidad Premium, así podrás añadir otro usuario. Cada uno accederá con su propia cuenta de email, lo que os permitirá personalizar vuestra experiencia en EL PAÍS.
¿Tienes una suscripción de empresa? Accede aquí para contratar más cuentas.
En el caso de no saber quién está usando tu cuenta, te recomendamos cambiar tu contraseña aquí.
Si decides continuar compartiendo tu cuenta, este mensaje se mostrará en tu dispositivo y en el de la otra persona que está usando tu cuenta de forma indefinida, afectando a tu experiencia de lectura. Puedes consultar aquí los términos y condiciones de la suscripción digital.