Fuselajes de avión en una sola pieza y ‘made in Murcia’
MTorres asegura que su tecnología es pionera en el mundo y reduce el peso del avión hasta un 30%
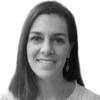
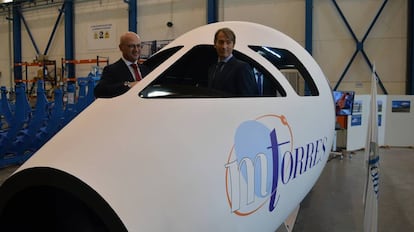
Reducir el peso de los aviones y, en consecuencia, los costes de combustible, es una de las preocupaciones constantes de la industria de la aviación. La multinacional española MTorres ha dado un paso más en ese objetivo desarrollando una tecnología que permite construir el fuselaje de un avión de una sola pieza, sin remaches, lo que supone reducir su peso entre un 10% y un 30%. Según la empresa, se trata de un sistema único a nivel mundial.
En seis meses, un equipo formado por una treintena de personas con el fundador de la empresa, Manuel Torres, a la cabeza, han desarrollado ese nuevo sistema, desde su diseño conceptual hasta la fabricación de un prototipo a escala con todas las condiciones reales idénticas a las que tendría un avión comercial. El proyecto, que se llevará como primicia a la feria aeronáutica de Le Bourget, en París, se ha presentado este viernes en Fuente Álamo (Murcia), donde la empresa tiene una de sus fábricas y en la que se ha llevado a cabo todo el proceso.
El responsable del proyecto, Sebastián Díaz, ha explicado que la nueva tecnología “cambia el paradigma de fabricación” actual de las aeronaves, que aunque han avanzado mucho en el empleo de materiales y tecnologías novedosas, mantienen “procesos de fabricación heredados de los primeros aviones de metal”. Eso se traduce en que cualquier fuselaje se construye a base de placas, de aluminio o de fibra de carbono, que tienen que ensamblarse con remaches. Entre 10.000 y 15.000 aproximadamente, la mayoría de los cuales se colocan de manera manual.
La propuesta de MTorres los elimina por completo con una estructura “monocasco”, de una sola pieza y en la que ni siquiera es necesario el uso de moldes de la industria tradicional. Así, en una primera fase, se construyen piezas que harían las veces de esos moldes, pero con la particularidad de que no hay que extraerlas, sino que quedan integradas en la estructura del fuselaje. Después, la estructura se encinta con fibra de carbono y todo el proceso se hace de forma automatizada.
La compañía está todavía evaluando cuánto reducirá este sistema los costes y calculan que será una cifra cuantiosa. “Si un avión tiene 15.000 remaches, calcule unos cuantos gramos de peso por cada uno de ellos, eso son muchos kilos, y en aviación un kilo vale su peso en oro”, ha señalado el director de la fábrica de MTorres en Fuente Álamo, David Doral. A eso hay que sumar el ahorro en tiempo y mano de obra: construir un modelo como el que llevarán a París supondría unos dos años de trabajo, que se han reducido a seis meses, asegura. En este caso, hasta la fibra de carbono es novedosa: la ha fabricado la propia empresa ahorrando en torno a un 50% sobre su coste de mercado.
Doral ha explicado que la compañía ya ha iniciado contactos con algunos de sus principales clientes, como Airbus o Boeing, para presentarles este “nuevo concepto para generar estructuras de una única pieza” y consideran que el éxito está garantizado.
Tu suscripción se está usando en otro dispositivo
¿Quieres añadir otro usuario a tu suscripción?
Si continúas leyendo en este dispositivo, no se podrá leer en el otro.
FlechaTu suscripción se está usando en otro dispositivo y solo puedes acceder a EL PAÍS desde un dispositivo a la vez.
Si quieres compartir tu cuenta, cambia tu suscripción a la modalidad Premium, así podrás añadir otro usuario. Cada uno accederá con su propia cuenta de email, lo que os permitirá personalizar vuestra experiencia en EL PAÍS.
En el caso de no saber quién está usando tu cuenta, te recomendamos cambiar tu contraseña aquí.
Si decides continuar compartiendo tu cuenta, este mensaje se mostrará en tu dispositivo y en el de la otra persona que está usando tu cuenta de forma indefinida, afectando a tu experiencia de lectura. Puedes consultar aquí los términos y condiciones de la suscripción digital.
Sobre la firma
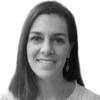