Así se fabrica un vehículo
Visitamos las tres plantas españolas más competitivas para su marca
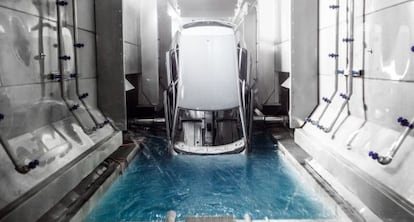
Yo nací Citroën. Esta frase de Juan, un trabajador de la fábrica de PSA de Vigo, que se incorporó a ella, siguiendo los pasos de su padre, cuando tenía 19 años (han transcurrido 22), refleja una de las características principales de la industria del automóvil en España: la involucración de sus plantillas. Probablemente la más determinante para obtener los éxitos logrados desde 2012, en plena crisis: los 15 modelos que las plantas nacionales han conseguido arrebatar a sus competidoras exteriores para garantizar su supervivencia con unas inversiones superiores a 9.000 millones de euros hasta 2019, si el Grupo Volkswagen (VW), en plena crisis por el escándalo de las emisiones contaminantes, ejecuta las que ha anunciado.
La mejora de la productividad de las fábricas de coches españolas tiene su eje central en la reducción de los costes del personal, tal y como se encargan de señalar cada uno de los representantes de las tres plantas que hemos visitado para este reportaje, punteras en competitividad dentro de sus propias marcas. También en el recorte del presupuesto de fabricación, los costes operativos, de consumo energético, de materiales…
El presidente del centro de VW en Navarra, Emilio Sáenz, lo resume así: “El equipo directivo, la muy buena relación con los sindicatos y la altísima motivación de la plantilla, que reacciona rápidamente ante cualquier problema, son las razones que han permitido que ganemos en calidad, productividad y costes”. Gracias a ello, esta factoría acaba de adjudicarse el nuevo modelo de Polo que saldrá al mercado en 2017 con unas inversiones de 1.000 millones de euros.
Claro que por el camino, los trabajadores se han dejado pelos en la gatera. “Desde que empezó la crisis han empeorado nuestras condiciones laborales”, se queja Miguel Ángel, un empleado de VW que ha visto automatizarse la planta pamplonica en los casi 30 años que lleva en ella. Las cifras de Anfac ponen de manifiesto el aquilatamiento del coste de la mano de obra: mientras en España ha crecido cerca del 10% entre 2008 y 2014, en Alemania, Francia e Italia ha subido más del doble.
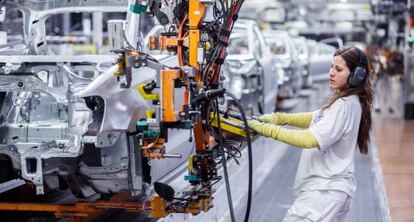
La flexibilidad de que hace gala el sector ha sido la clave para que en los peores momentos de la recesión, el motor haya destruido mucho menos empleo que el resto de la industria. Ha sido posible mediante los expedientes de regulación de empleo temporales, la distribución irregular de jornadas y los contratos a tiempo parcial, indica el director de relaciones sociales de PSA Vigo, Pedro Rodríguez. “En este mercado tan complejo en el que tenemos que competir con todos, nuestra competencia más cercana son las otras fábricas de nuestro propio grupo. En el caso de Vigo, que produce seis modelos y 1.800 unidades diarias; la planta de PSA de Eslovenia”. Para ganar el modelo K9, que se lanzará en 2018, “había que reducir las inversiones asociadas a él, los costes salariales, de la flexibilidad y del proceso logístico”, añade Rodríguez.
El grupo francés PSA ha puesto en marcha el plan denominado Fábrica excelente que lleva aparejada la reconversión de las factorías, iniciada por Francia, donde durante la crisis ya cerró una planta (igual que Ford clausuró las de Reino Unido y Bélgica). Un programa que tiene como objetivo reducir en 500 euros el precio de producción del automóvil (que puede oscilar entre 500 y 2.000 euros en Europa) en una carrera hasta 2018 que no afecta tanto al centro de Vigo, dado lo aquilatados que son sus costes, según sus responsables. El plan de Peugeot Citroën incluye optimizar los procesos logísticos y que las compras a los proveedores del Este de Europa se dupliquen. Con una guía de 30 indicadores, PSA compara sus factorías mundiales (por coste de mano de obra, energético, de aprovisionamiento, de distribución, ayudas de la Administración...) y así es cómo decide sus inversiones, en función de qué planta esté más cerca de ser excelente.
Cada fábrica tiene su forma de hacer. Mientras que en Ford Almussafes o en PSA Vigo modulan sus ritmos de producción y sus turnos de trabajo (la valenciana acaba de recuperar el turno de noche y la gallega fabrica 35 vehículos por hora en vez de 50, su máximo), en VW Navarra prefieren trabajar a pleno rendimiento. “Estamos a tope de capacidad diaria. Producimos 1.450 coches al día, lo que quiere decir que cada 56 segundos vendemos un vehículo. Flexibilizamos en días de trabajo, cuando en otras fábricas lo hacen suprimiendo turnos o reduciendo la velocidad. Nosotros, si no tenemos coches, cerramos. Porque, una vez que arrancas la planta, los costes fijos empiezan a contar, y son los mismos si estás a pleno rendimiento o no”, explica Miguel Ángel Grijalba, responsable de producción de VW Navarra.
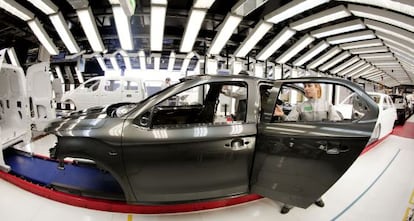
El engranaje
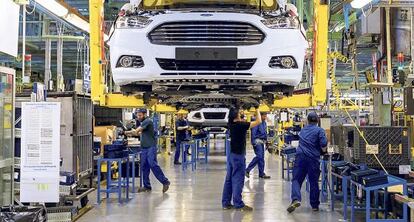
Cuando uno entra en una fábrica de coches, lo primero que impresiona es el tamaño y la cantidad de robots que hacen posible este engranaje milimétricamente medido. En esto Ford Almussafes se lleva la palma, con 800.000 metros cuadrados construidos en una decena de naves y 2.040 androides. Estas máquinas están presentes en casi todo el proceso de producción, aunque son vitales en las tareas más pesadas, las del área de prensa y chapistería. Es con la que arranca la fabricación. Gigantescas bobinas de acero son cortadas y prensadas con matrices adaptadas para cada parte de la carrocería del vehículo en un procedimiento plenamente automatizado donde el hombre es un mero controlador. Y en el que sorprende ver el escaso grosor (0,7 milímetros) de la chapa con que se hace un coche. Casi parece de juguete.
Después las piezas se van ensamblando entre sí mediante el proceso de soldadura, también muy mecanizado, aunque con más personal que el anterior. Son nada menos que unas 800 piezas las que se manejan.
Con el esqueleto ya montado, los coches pasan a la siguiente etapa, la más sensible: la pintura. Solo vemos esta zona, que está presurizada y, por tanto, es de acceso restringido, en la planta de Navarra.
Una carrocería tras otra van saltando a una piscina que sirve para eliminar la suciedad recogida durante el ensamblaje. Tras el baño, se preparan con ácidos antes de darles el color. Los robots, agrupados de cuatro en cuatro o de cinco en cinco en cubículos de cristal, reciben los coches y protegen con masilla sus partes delicadas. Están tapados para no mancharse con el pulverizado. De estación en estación, un autómata dispara su pintura sobre una aleta delantera, el otro sobre una puerta, el otro sobre el capó… En plena sincronía, los colores van cambiando conforme a la lectura de los códigos de barras que acompañan a las carcasas de los vehículos. Luego pasan a un horno a 65 grados de temperatura para que la pintura se seque y se puedan barnizar y pulir. El proceso acaba en un arco de luces donde se comprueba el acabado.
Y se inicia el montaje, uno de cuyos momentos esenciales es la denominada boda, donde el motor de propulsión con la caja de cambios incorporada y su carrocería se funden en un todo. Aquí la mano de hombre se hace mucho más necesaria.
Unas partes del auto llegan a la cadena de montaje por el suelo, otras por el aire en un perfecto encadenamiento secuencial que, gracias a los códigos de barras, permiten a robots y trabajadores encajar en cada modelo las piezas que necesita. El vehículo pasa un minuto por cada puesto, al menos en Vigo. Primero se montan los interiores, después los bajos, las enormes lunas que el robot coloca en seis movimientos y así hasta un total de 4.500 piezas.
En general, los vehículos de una misma marca suelen compartir pisos, motor, climatización, escapes, asientos… “todo lo que el cliente no ve”, dicen en ellas. Sin embargo, cuando se trata de carrocerías o interiores de la máquina, cada una es un mundo. Bien lo saben en Ford, en cuya modernizada factoría tras hacerse con tres nuevos modelos (los monovolúmenes S-Max y Galaxy y el Mondeo Vignale) y unas inversiones de 2.300 millones de euros, se producen cinco vehículos diferentes con equipamientos distintos. “Somos la primera planta de Ford en Europa. Y en el mundo, nadie fabrica cinco modelos. Y menos aún con 360 carrocerías distintas, como hacemos aquí para la Transit Connect”, presume Helios Álvarez, gerente de prensas y carrocerías de Almussafes. “Hemos pasado de manejar 8.000 piezas en 2008 a las 18.000 actuales”, apoya Luis Rafecas, su homólogo en el área de logística. La fábrica hace 1.800 unidades diarias, aunque el año que viene pretende llegar a 2.100.
Fallos in situ
Las multiplataformas, como la que va a instalar VW en Navarra, o plataformas modulares o compartidas, como las que tienen en Vigo PSA y Ford en Almussafes, permiten que en una misma cadena de montaje se produzcan distintos modelos de coches, y el sistema de kitting, mediante el cual el conjunto de piezas que precisa cada vehículo personalizado llegan a él ya seleccionadas, son dos de las innovaciones recientemente introducidas en el sector y que han permitido a las plantas españolas mejorar su eficiencia. Cada minuto cuenta.
Por eso cada equipo se ocupa de la parte de la fabricación que corresponda y también de su mantenimiento. Es lo que en Ford llaman equipos integrados, y que sirve para que, a medida que el coche va pasando por las diferentes estaciones, se puedan detectar anomalías y subsanarlas en ese momento in situ, antes de que la línea continúe y se haga más caro arreglarlas, indica Grijalba. España es pionera en ello dentro del sector, dice Helios Álvarez.
Y suelta la coletilla que se repite una y otra vez en Almussafes: “Copiamos con orgullo”. Se refiere a las técnicas de Toyota enfocadas a la reducción de costes y el mantenimiento autónomo, lo que revierte en mayor tiempo de producción, el denominado lean manufacturing. En PSA lo traducen por “contentos de copiar”.
Con el operario responsabilizándose de la calidad, “hemos pasado de que el ‘bueno directo’ afectase al 85% de los coches, al 88% hace tres semanas”, explican en Vigo. En Navarra, la cifra es del 98,5%, según Grijalba.
Pero finalmente todos los coches pasan por una revisión de calidad que, dependiendo de las plantas, es más o menos exhaustiva. Cierres, prueba de agua, faros… En alguna de ellas supone su rodaje en la pista de pruebas uno por uno. Es el momento del arrancado, el que culmina un proceso de fabricación que ha durado entre 20 y 36 horas. Y es del que presumen los orgullosos trabajadores de la industria del automóvil.
Cómo hemos cambiado...
A Helios Álvarez le acaban de entregar la placa que conmemora sus 30 años en Ford. Al frente del área de prensa y carrocerías, ha pasado por distintos puestos y países desde entonces. Pero celebra esos tres decenios en la fábrica que le ha visto crecer, donde trabajó su padre y le gustaría que lo hiciese su hijo. Álvarez llama brutal al cambio que ha experimentado la planta desde 1985. Y reflexiona: “Hace treinta años no teníamos ni ordenadores. Tampoco robots. Hacíamos un solo modelo y ahora son cinco”. “Cogíamos la chapa con pinzas de soldadura manuales, mientras que ahora lo hace un robot. Se ha mecanizado en trabajo y hacemos menos esfuerzo físico”, reconoce Miguel Ángel, con casi la misma antigüedad en VW.
En estas tres décadas se ha ganado mucho en precisión y en flexibilidad, explica Álvarez, lo que implica que, “aunque hoy hagamos cerca de 400 Kuga, si nos piden el doble, podemos adaptarnos. Y es precisamente esta capacidad de estar en constante evolución, propia de España y no de otros países, la que nos ha hecho progresar junto con el aumento de la cualificación de los trabajadores”.
Las relaciones laborales han mejorado mucho desde los años ochenta, resalta Jesús, que cumple tres décadas en VW. Y lo certifica su directora de recursos humanos, la alemana Susanne Dellit, para quien España es actualmente más flexible que Alemania, de quien aprendió. “La preocupación por la comodidad de los trabajadores en la línea, por la ergonomía es nueva. Hoy, por ejemplo, los interiores de los coches se montan con el operario sentado en un asiento móvil”, continúa Jesús.
Los cambios son incuestionables. Y tantos... Luis Rafecas, en cuya placa conmemorativa ya se ven 35 de sus 39 años de antigüedad en Ford, los lleva a su campo, el de la logística. “En 1985 nuestros proveedores eran locales. Ahora están muy lejos. En EE UU, Europa del Este, China, América Latina... y, a medida que ellos se alejan, los costes aumentan”. Los fabricantes quieren atraerlos hacia ellos, de hecho, en Almussafes un tren une la factoría y la zona de proveedores. Además, tanto Ford como PSA planean llevar sus centrales de compras a Marruecos.
Tu suscripción se está usando en otro dispositivo
¿Quieres añadir otro usuario a tu suscripción?
Si continúas leyendo en este dispositivo, no se podrá leer en el otro.
FlechaTu suscripción se está usando en otro dispositivo y solo puedes acceder a EL PAÍS desde un dispositivo a la vez.
Si quieres compartir tu cuenta, cambia tu suscripción a la modalidad Premium, así podrás añadir otro usuario. Cada uno accederá con su propia cuenta de email, lo que os permitirá personalizar vuestra experiencia en EL PAÍS.
¿Tienes una suscripción de empresa? Accede aquí para contratar más cuentas.
En el caso de no saber quién está usando tu cuenta, te recomendamos cambiar tu contraseña aquí.
Si decides continuar compartiendo tu cuenta, este mensaje se mostrará en tu dispositivo y en el de la otra persona que está usando tu cuenta de forma indefinida, afectando a tu experiencia de lectura. Puedes consultar aquí los términos y condiciones de la suscripción digital.
Sobre la firma
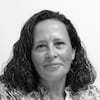